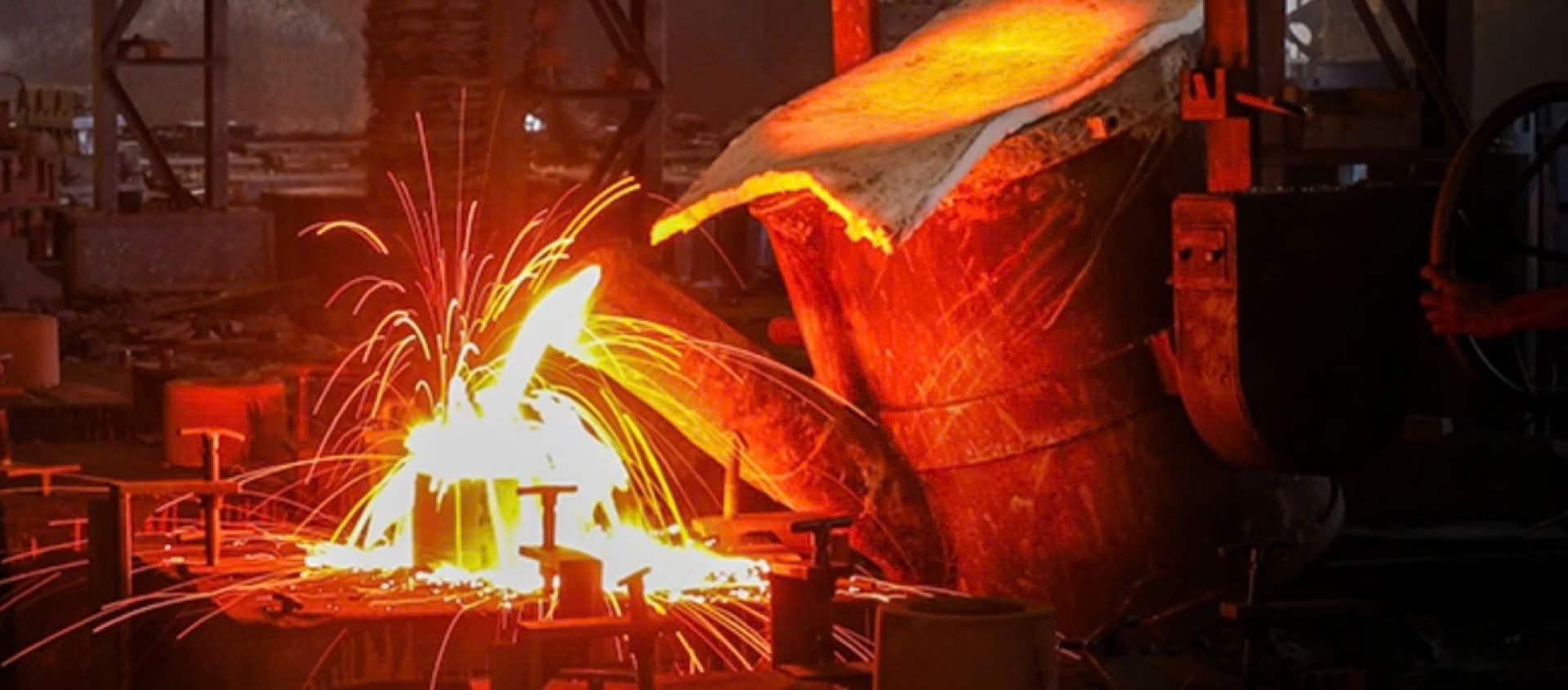
CASTING
I. Casting parts in Vietnam
The metal casting industry in Vietnam has experienced significant growth and transformation over the past few decades. Initially, the industry was largely characterized by small, traditional foundries that relied on manual techniques and local materials. However, with the advent of modernization and increased foreign investment, Vietnam has seen the establishment of more sophisticated casting facilities equipped with advanced technologies. This shift has not only improved the quality and precision of cast products but has also expanded the range of applications across various sectors, including automotive, machinery, and construction. Moreover, the government's focus on industrialization and export promotion has further fueled the industry's development, leading to a more competitive landscape.
I. Main casting methods
1. Fresh sand casting, Plastic sand casting
Fresh sand casting is the most common casting method in Vietnam, followed by furan sand casting. The sand used for molds is often mined from Van Hai - Quang Ninh (quartz sand), Nui Thanh - Quang Nam, Ba Don - Quang Binh, Ha Tinh. After being mined and processed, most of the quartz sand will be used in the glass and construction glass industry, while the remainder is used in other industrial sectors, including casting.
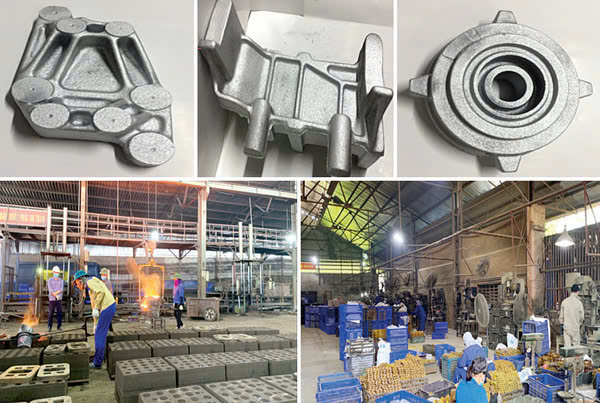
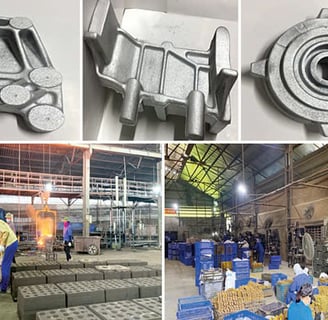
2. Casting mold
- Lost wax casting is one of the oldest metal forming techniques known, dating back 6,000 years, and is used to cast metal shapes ranging from simple to complex using various metals (such as gold, silver, bronze, or stainless steel).
- The metal casting is shaped through a process called "lost wax". The original wax model is made to resemble the casting and can burn away at low temperatures. After obtaining the wax model, a ceramic mold is created for metal casting. The metal is poured into the mold and solidifies until the casting shape is fully formed. Due to the advantages of precision and quality that lost wax casting provides, it has become the preferred choice for engineers in industries that require high accuracy.
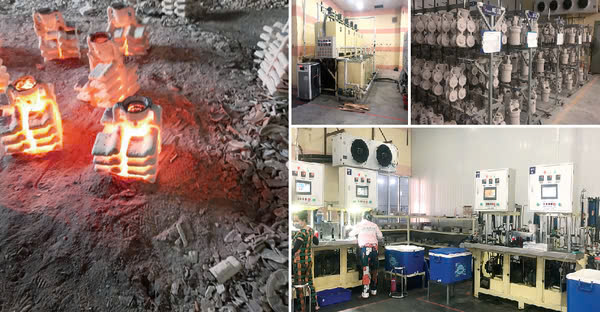
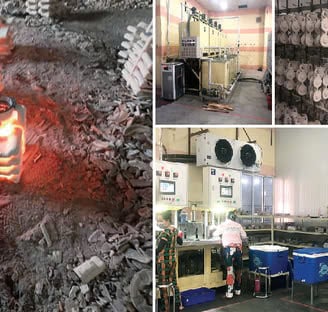
3.Pressure casting.
Casting is a method of manufacturing blanks in which molten metal is forced under high pressure. Essentially, it is the process of filling a mold with liquid metal that has a predetermined shape and size, where the liquid metal is held in place by a strong compressive force until it solidifies completely, forming a shape corresponding to the mold; this is called a cast object. If the cast object is further processed, it is referred to as a cast blank.
3.1 Hot chamber pressure casting: Casting is a method of manufacturing blanks in which molten metal is forced under high pressure. Essentially, it is the process of filling a mold with liquid metal that has a predetermined shape and size, where the liquid metal is held in place by a strong compressive force until it solidifies completely, forming a shape corresponding to the mold; this is called a cast object. If the cast object is further processed, it is referred to as a cast blank.
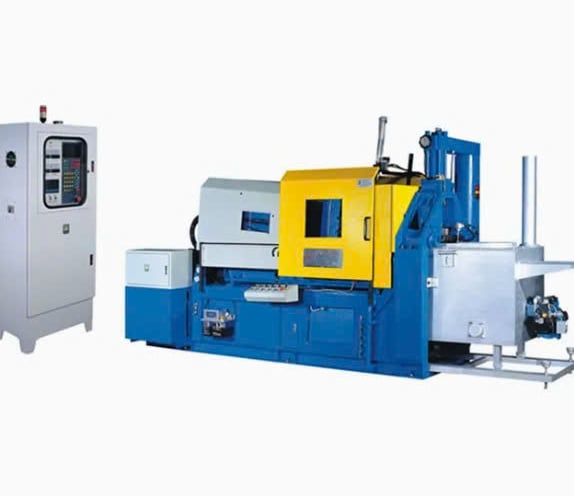
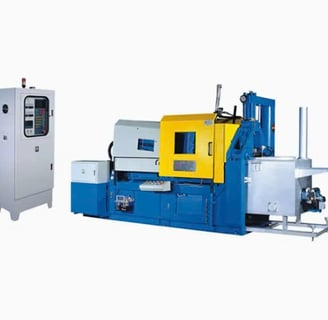
3.2. Cold chamber die casting: In contrast to hot chamber die casting, the molten metal is melted in a separate furnace and then poured into the shot sleeve, where high pressure pushes the piston to inject the metal directly into the mold cavity.
Cold chamber die casting is used for metals with high melting points such as aluminum, copper, and magnesium.
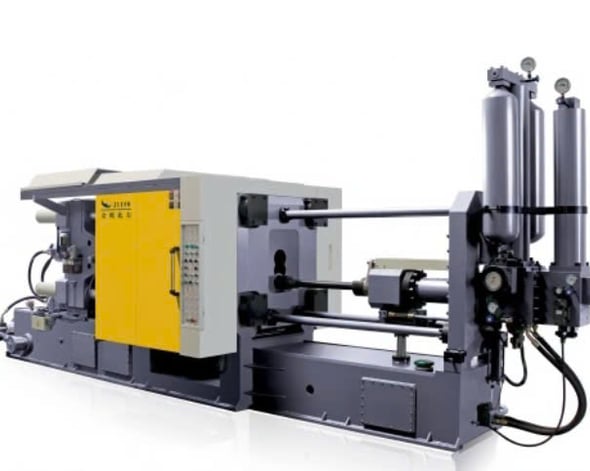
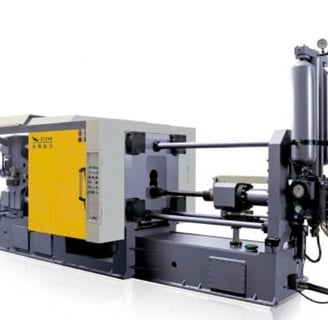
Contact Us For A Free Quote Today
Service
We connect you with the best factory.
Contact
Support
Email: tuan@dicejsc.com
Phone: +84-986-928-916
© 2024. All rights reserved/ Managed by Dao Tuan
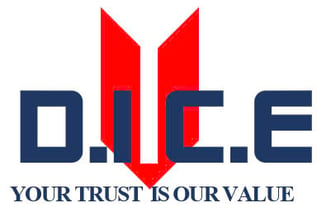
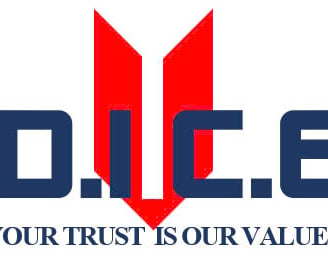